
The printing phase is followed by a series of in-house crucial steps that are necessary for a fabric to be finished.
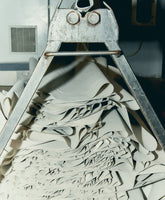
Once printed, the fabric is steamed, washed and treated with detergents and products based on product-type dye formulations.
Once printed, the fabric is steamed, washed and treated with detergents and products based on product-type dye formulations.
Read More
Read Less
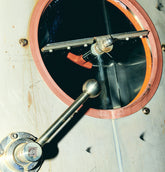
Our steaming systems feature a technology that uses less steam per unit of fabric treated, which increases production process's sustainability.
Our steaming systems feature a technology that uses less steam per unit of fabric treated, which increases production process's sustainability.
Read More
Read Less
The printed fabric goes through a steaming machine which is a closed chamber. It is held there for different times which depend on the dye type. Inside the chamber, saturated steam reaches a temperature of approximately 105°C. The steam allows the colour to be fixed to the fabric, causing the printing formulation components to react.
The printed fabric goes through a steaming machine which is a closed chamber. It is held there for different times which depend on the dye type. Inside the chamber, saturated steam reaches a temperature of approximately 105°C. The steam allows the colour to be fixed to the fabric, causing the printing formulation components to react.
Read More
Read Less
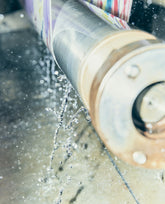
Each of our fabrics is washed with water to remove impurities. The detergents are formulated according to the dye type and ensure that excess colour does not redeposit on the fabric.
Each of our fabrics is washed with water to remove impurities. The detergents are formulated according to the dye type and ensure that excess colour does not redeposit on the fabric.
Read More
Read Less
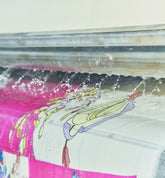
Different detergents for reactive or acid dyes are used depending on whether it is screen or digital printing.
Different detergents for reactive or acid dyes are used depending on whether it is screen or digital printing.
Read More
Read Less
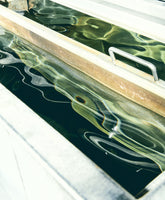
Another crucial factor in the washing process is the water temperature, which varies between 45° and 90°C depending on the dyes. With our new co-generator, heat can be recovered and used for the washing process.
Another crucial factor in the washing process is the water temperature, which varies between 45° and 90°C depending on the dyes. With our new co-generator, heat can be recovered and used for the washing process.
Read More
Read Less
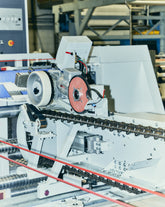
The steamed and washed fabric goes through a machine called stenter which keeps it taut and firm. The fabric in the stenter is impregnated with products based on precise formulations to provide the final "tactile effect", which is crucial in the textile field.
The steamed and washed fabric goes through a machine called stenter which keeps it taut and firm. The fabric in the stenter is impregnated with products based on precise formulations to provide the final "tactile effect", which is crucial in the textile field.
Read More
Read Less
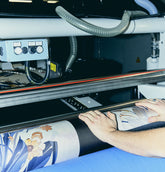
The finishing phase is fundamental and gives the fabric its final tactile effect, solidity, stability and resistance. This process takes place mechanically and chemically to achieve a wide result diversification.
The finishing phase is fundamental and gives the fabric its final tactile effect, solidity, stability and resistance. This process takes place mechanically and chemically to achieve a wide result diversification.
Read More
Read Less

After the stenter, the fabric may undergo other mechanical processes such as the rolling press, which crushes the fabric between two cylinders to improve the starching, or the "airo" machine which exploits the action of air and some additives to obtain extremely soft fabrics.
After the stenter, the fabric may undergo other mechanical processes such as the rolling press, which crushes the fabric between two cylinders to improve the starching, or the "airo" machine which exploits the action of air and some additives to obtain extremely soft fabrics.
Read More
Read Less